6300 Bury Drive
Eden Prairie, MN 55346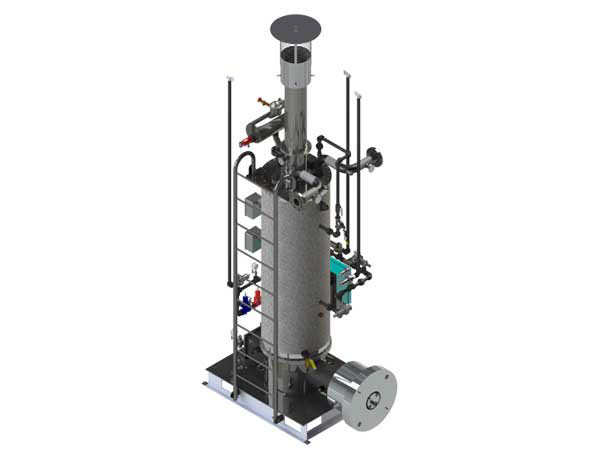
TERI Vertical Indirect Fired Water-bath Heaters
TERI vertical indirect-fired water bath heaters are an aesthetically pleasing and environmentally safe addition to TERI's popular horizontal water bath heater line.
The complete vertical heater system consists of the following components, each designed to meet specific design criteria:
- The process coil, which is designed in accordance with API 12 K or ASME Section VIII Division 1 code requirements
- The firetube which efficiently transfers heat into the surrounding heat media
- The heater shell, which is an atmospheric vessel designed in accordance with API 12 K requirements
- The heat media, which is commonly a mixture of glycol and water which is blended to a consistency to provide for proper freeze protection
TERI Vertical Indirect-Fired Water Bath Heaters:
- Are not under a vacuum system
- Utilize stacks that are not necessarily as tall as horizontal-style heater stacks
TERI Vertical Indirect Fired Water Bath Heater Applications
- Heating natural gas prior to pressure reduction to eliminate frost formation downstream of regulation
- Preventing hydrate formation in well stream fluids
- Heating well stream fluids prior to phase separation
Features
- Higher Thermal Efficiency (75%-85%)
- Small footprint package
- Quiet burner assembly
- Pneumatic instrumentation
- Forklift pockets and lifting lugs for ease of installation
- Fully enclosed controls
Available Options
- Sophisticated remote control and monitoring equipment
- Flame-safeguard assemblies including pneumatic 120VAC, 24VDC, 12VDC, or solar power
- Manual or automatic pilot ignition designs
- Shell treated with water-soluble rust prevention coating
- Hot-dipped galvanized heater skids, ladders, and platforms
- Other customized solutions as required by the application
Standard Sizes
100,000 BTU/Hour (3'x4' Base x 6'4" Tall)
200,000 BTU/Hour (4'x5' Base x 7'6" Tall)
300,000 BTU/Hour (4'x5' Base x 8'8" Tall)
400,000 BTU/Hour (4'x5' Base x 9'10" Tall)
500,000 BTU/Hour (5'x6' Base x 11' Tall)
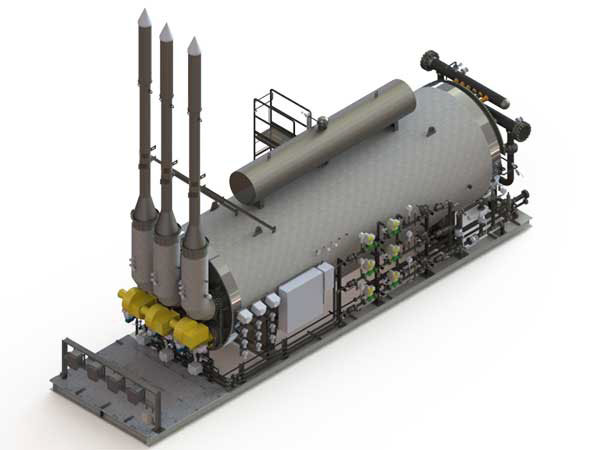
TERI Horizonal Forced Draft Water-Bath Heaters
TERI Horizontal Forced Draft water-bath heaters are commonly used in applications where process temperatures do not exceed 170°F, including utility, gas processing, refining of oil and gas, and other industrial applications. Our Forced Draft Horizontal Heaters can be designed in single, double, or triple-burner configurations. With capacities from 1 MM Btu/hr. up to 15 MM Btu/hr., our expert team can conceive and construct the right TERI Horizontal Heater for your needs.
For low-emission requirements, TERI forced draft heaters offer an ideal solution to reduce dead gas film along the tube walls and provide superior burner control, making fine-tuning the air/fuel ratio possible to achieve efficient combustion and lower emissions.
TERI Horizontal Forced Draft Heater Applications
- Heating natural gas prior to pressure reduction to eliminate hydrate formation downstream of expansion valving
- Heating well stream fluids prior to phase separation
- Heating process streams to maintain fluid viscosity at a minimum to reduce HP pumping requirements
- Heating turbine fuel gases to meet manufacturer's temperature requirements
- Vaporization of liquid propane
Features
- Plasma-cut, TERI-fabricated components
- Individually removable firetubes designed to transfer heat efficiently into the surrounding heat media and minimize flue gas friction losses
- Process coil designed in accordance with API 12K or ASME Section VIII Division 1 code requirements
- 304 SS flue gas stack or stacks designed to provide positive flue gas flow (draft) by overcoming the friction losses in the complete combustion system
- Stack clean-out tee
- Flue gas stack anti-reverse draft diverters with train cap and bird screens
- Essential electric and pneumatic in addition to PLC control systems
- Multi-mitered firetube bends (no single miter cut to greater than 22.5°)
- Positive seal flange designs
- Bath liquid expansion tank designed to contain 7% of the total bath media and 100% of the expanded bath media from a temperature of 40°F to the maximum operating temperature
- Bath liquid level gauge and temperature indicator
- Shell designed in accordance with API 12K
- Fuel gas train designed to API 12K standards, with larger duty heaters also meeting ASME standards
- 100% radiography inspection of process coil welds
Available Options
- Sophisticated remote control and monitoring equipment
- Flame-safeguard assemblies including pneumatic 120VAC, 24VDC, 12VDC, or solar power
- Manual or automatic pilot ignition designs
- Cushioned (electrically insulated) process coil supports
- Shell treated with water-soluble rust prevention coating
- Customized heater supports to meet existing pier locations
- Hot-dipped galvanized heater skids, ladders, and platforms
- Other customized solutions as required by the application
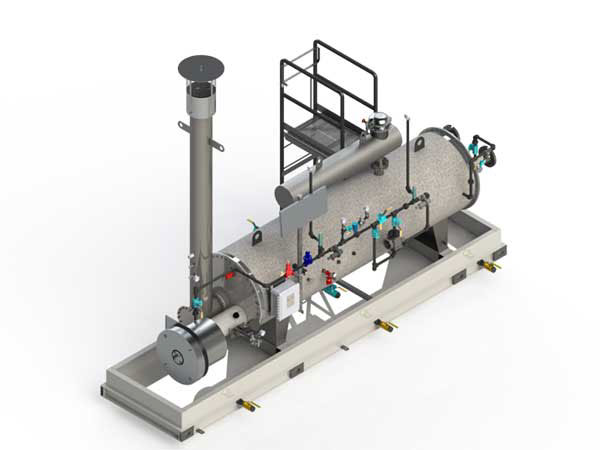
TERI Natural Draft Horizontal Heaters
TERI Natural Draft Horizontal Heaters are ideal for remote locations and locations with limited power supply. They are custom designed and engineered for each application and can be designed in single, double, or triple-burner configurations.
TERI horizontal water bath heaters are commonly used in applications where process temperatures do not exceed 170°F, including utility, gas processing, refining of oil, gas, and other industrial applications.
With capacities from 0.3 MMBtu/hr to over 15 MMBtu/hr, our expert team can conceive and construct the right TERI Horizontal Heater for your needs. With available options in both forced draft and natural draft models, TERI heaters can accommodate any working conditions, environmental compliance, and power availability.
TERI Horizontal Indirect Fired Water Bath Heater Applications
- Heating natural gas prior to pressure reduction to prevent freezing of valving and instrumentation
- Heating well stream fluids prior to phase separation
- Heating of high-viscosity fluids to reduce pumping pressures
- Heating fuel gas at power generation stations
- Heating at compressor stations
- Heating high-pressure hydrocarbon gas streams
- Vaporization of liquid propane
- Reboiler heating
Features
- Designed and built in accordance with API 12K
- Removable firetube and coil bundle
- 100% radiography on process coil welds
- Process coil built to ASME VIII Div 1 code requirements
- National board stamped
- Pilot-in-a-drawer: easy access, quick removable pilot assembly
- 304 Stainless Steel stacks
- ASME CSD-1 fuel gas trains, custom designs available including NFPA 86 and 87
Available Options
- Custom coil configurations to meet footprint and space constraints
- Customized heater supports to meet existing pier locations
- Shell treated with water-soluble rust prevention coating
- Hot-dipped galvanized skids, ladders, and platforms
- 110% containment skids with drain valves
- Pneumatic, electric, or combination equipment operation controls
- High pressure coil ratings up to 10,000 psig
- Flame-safeguard assemblies including pneumatic, 120VAC, 24VDC, 12VDC, or solar power
- Manual, pushbutton, automatic relighters, and Burner Management Systems (BMS)
- Remote control and monitoring
- Low NOx and Ultra Low NOx
- PLC based controls
- HMI displays
- Low noise flame arrestor modifications
- Flame arrestor draft controls
- Stack insulation
- Unobstructed discharge stack design for improved dispersion of emissions
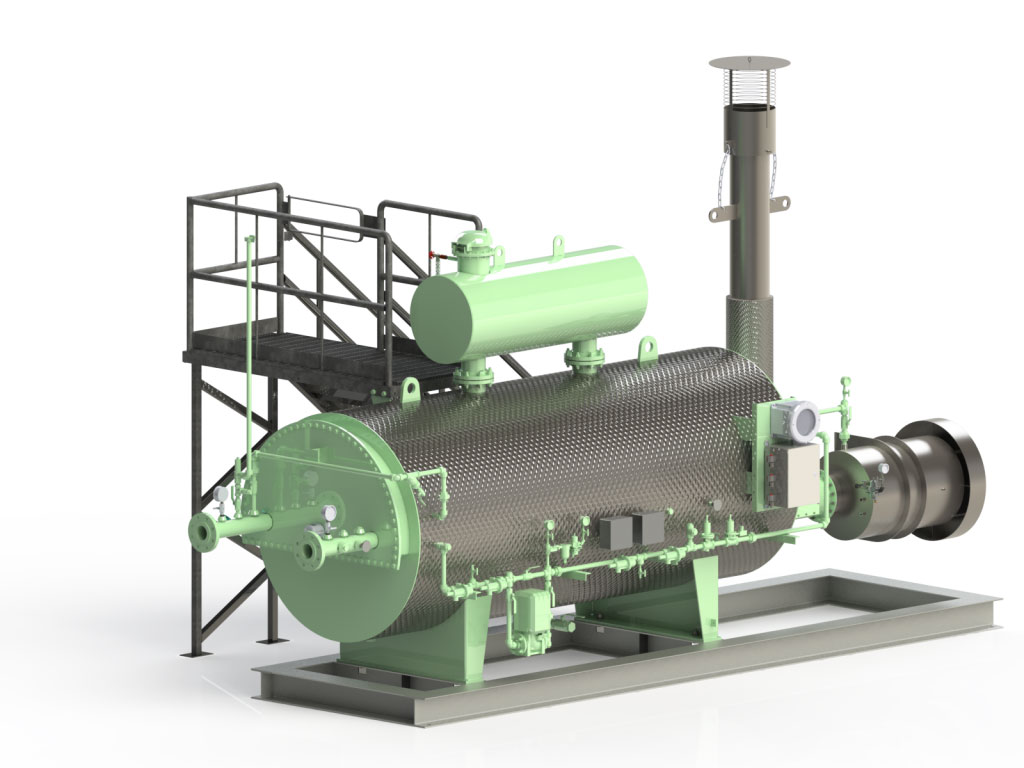
TERI Fuel Gas Heaters
TERI Fuel Gas Heaters are ideal for applications where sensible heat input is required or where superheating gas above hydrocarbon and water saturation dew points, and elemental sulfur control is needed.
TERI Fuel Gas Heaters are sized for dedicated temperature ranges based on customer specifications and pair well with gas turbines such as solar turbines. They are PLC controlled to coordinate with gas turbines for seamless operation and stable fuel gas temperature control. Available in slip-stream configuration when a wide gas temperature control range is acceptable, or in a tempering control configuration when a tighter gas temperature control is required.
TERI Fuel Gas Heater Applications
- Superheating gas
- Fuel gas dew point control
- Elemental sulfur control
- Heating at compressor stations
- Heating at power generation stations
- Heating at cogen plants
- Heating at combined cycle power plant
Features
- Designed and built in accordance with API 12K
- Wide or tight gas temperature control ranges
- Removable firetube and coil bundle
- 100% radiography on process coil welds
- Process coil built to ASME VIII Div 1. National board stamped
- 304 Stainless Steel stacks
- ASME CSD-1 fuel gas trains, custom designs available including
- NFPA 86 and 87
- PLC controlled for coordination with gas turbine
- Designed, fabricated, and fully tested (including shop-fired) all in-house by OGI
Available Options
- Sophisticated remote control and monitoring equipment
- Flame-safeguard assemblies including pneumatic 120VAC, 24VDC, 12VDC, or solar power
- Manual or automatic pilot ignition designs
- Cushioned (electrically insulated) process coil supports
- Shell treated with water-soluble rust prevention coating
- Customized heater supports to meet existing pier locations
- Hot-dipped galvanized heater skids, ladders, and platforms
- Other customized solutions as required by the application